
This can be very damaging, causing severe erosion of the pump’s components. The vapour condenses and the bubbles implode, releasing, locally, huge amounts of energy. The formation of bubbles leads to a loss in throughput and increased vibration and noise but the big danger is when the bubbles pass on into a section of the pump at higher pressure. If the pressure of the fluid at any point in the pump is lower than its vapour pressure, it will literally boil, forming vapour bubbles within the pump. The fluid’s pressure increases again when it is expelled. In a positive displacement pump, the fluid’s pressure drops when it is drawn, essentially from rest, into the cylinder. In a centrifugal pump, for example, there is a large drop in pressure at the impeller and an increase again within its vanes (see diagram).
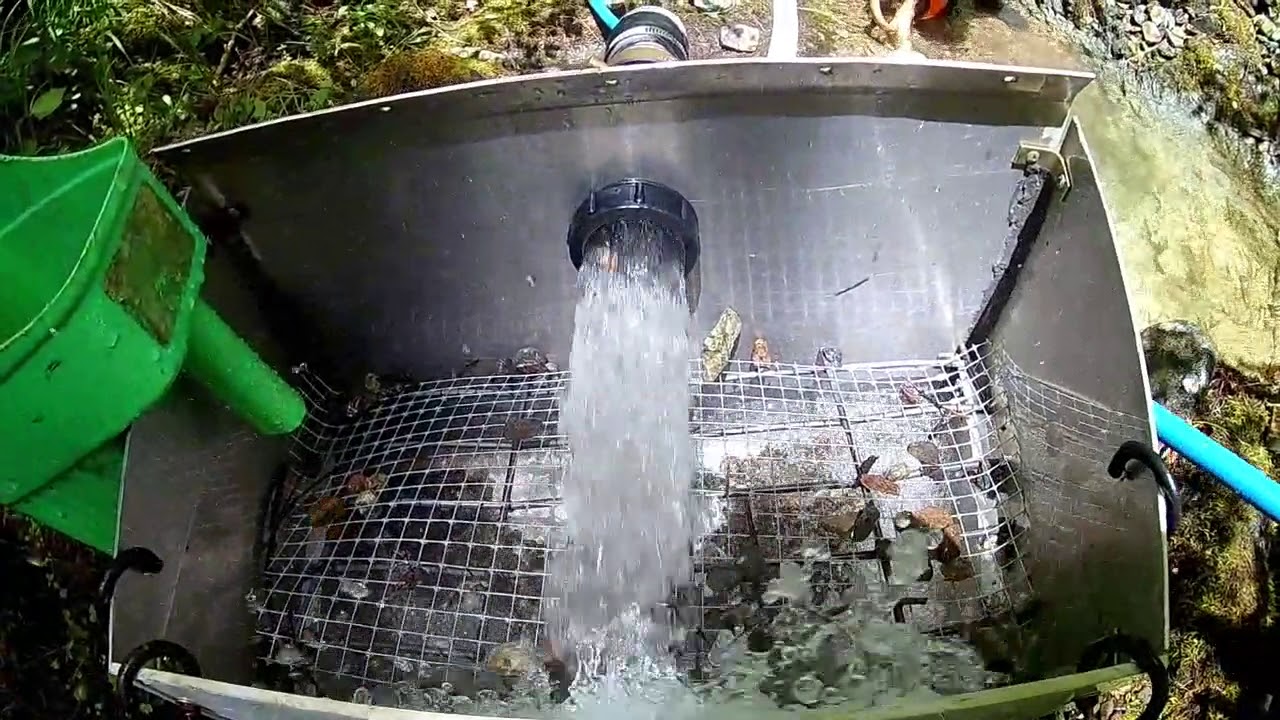
This arises from many properties of the system: the throughput rate, head pressure, friction losses both inside the pump and across the system as a whole. If water, for example, is subjected to a sufficient drop in pressure at room temperature, it will boil.Īcross any pumping system there is a complex pressure profile. Poor installation of pipework and other components.Ī liquid’s boiling point corresponds to the temperature at which its vapour pressure is the same as the pressure of its environment. Suspended solids resulting in increased erosion. Narrow pipes and constrictions producing noise, turbulence and friction losses.Īir or vapour entrainment causing noise, friction and loss of performance. Insufficient fluid pressure leading to cavitation within the pump. The root cause of many pump problems and failures can be traced to poor upstream, suction-side, pipeline design.
